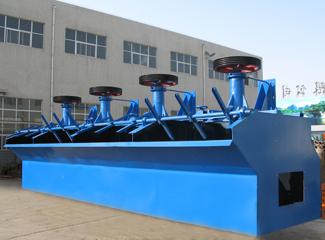
To realize the separation of the ore particles, the surface of the ore particles should have different wetability and there should be some bubbles with a certain quantity and quali...
To realize the separation of the ore particles, the surface of the ore particles should have different wetability and there should be some bubbles with a certain quantity and quality, and there should also be suitable machinery to separate them into products with different properties and quality, such machinery is flotation cell, which can also be called flotation machine, flotation-cell, flotation plant and flotation separator. Flotation cells are important machines to realize the flotation separation process and the quality of the flotation separation process is not only related to the reagent and the technology, but related to the performance of the flotation machine.
The structure of flotation machine: this machine is mainly composed of pulp chute, mixing device, air charging system, mineralized bubble discharging device and electro motor.
(1) Pulp chute: It has pulp feeding mouth and the gate device used for adjusting the liquid level and it is mainly composed of mainly composed by the chute body which is melt by the steel board and gate melt by the steel board and steel rod.
(2) Mixing device: It is mainly used for mixing the pulp in order to prevent the mineral sand to deposit on the chute, and it is mainly composed by the belt wheel, impeller, vertical shaft and the impeller is made of the anti-abrasion rubber.
(3) Air charging system: It is mainly composed by the inlet air pipe. When the impeller rotates, there will produce negative pressure inside the impeller chamber in order to absorb air through the hollow pump line and disperse the pulp in order to form a bubble group. This kind of pulp with large quantity of bubbles will be thrown to the stator fast by the rotary force of the impeller and further mineralize the bubbles in the pulp, and the rotary movement that is meant to eliminate the pulp flow in the flotation cell will cause large quantity of microvesicle and provide necessary condition for the flotation process.
(4) Mineralized foam discharging device: This device is mainly used for scarping the foam floating on the cell and it is mainly composed by the reducer driven by the electric motor and scrapper driven by the reducer.
Mix the mashed rocks with water and necessary reagent in the mixing chute, and inject them to the pulp chute. Lead air to the pulp to make it form large quantities of bubbles, and some mineral particles that are difficult to get moist in water and that are generally called hydrophobic mineral particles will stick on the bubbles and float with the bubbles to the surface of the pulp to form mineralized bubble layer, and some other mineral particles that are easy to get moist in water and that are called hydrophilic mineral particles do not stick on the bubbles but stay in the pulp to discharge the mineralized bubbles containing specific minerals, thus completing the separation process.
Technical Parameters of SF Series Flotation Machine
Category | Specification Model |
Effective cubage (m³) |
Processing capacity (m³/min) |
Main shaft loam board | Dimensions (L×W×H) (m) |
Single trough Weight (t) |
|||
Power(kw) | Rotate Speed(r/min) | Rotate Speed(r/min) | Power(kw) | ||||||
XJK type flotation machine |
XJK-0.35 | 0.35 | 0.18-0.4 | 1.5 | 483 | 25 | 1.1 | 0.7×0.7×0.7 | 0.5 |
XJK-0.62 | 0.62 | 0.3-0.9 | 3.0 | 400 | 25 | 1.1 | 0.90×0.82×0.85 | 1.0 | |
XJK-1.1 | 1.1 | 0.6-1.6 | 5.5 | 330 | 25 | 1.1 | 1.1×1.1×1 | 1.4 | |
XJK-2.8 | 2.8 | 1.5-3.5 | 11 | 280 | 25 | 1.1 | 1.75×1.6×1.1 | 2.5 | |
XJK-5.8 | 5.8 | 5-7 | 22 | 240 | 25 | 1.5 | 2.2×2.2×1.2 | 3.6 | |
SF type flotation machine |
SF-0.37 | 0.37 | 0.2-0.4 | 1.5 | 386 | 25 | 1.1 | 0.7×0.7×0.75 | 0.5 |
SF-0.7 | 0.7 | 0.3-0.9 | 3 | 400 | 25 | 1.1 | 0.9×0.82×0.95 | 1.0 | |
SF-1.2 | 1.2 | 0.6-1.6 | 5.5 | 330 | 25 | 1.1 | 1.1×1.1×1.1 | 1.9 | |
SF-2.8 | 2.8 | 1.5-3.5 | 11 | 268 | 25 | 1.1 | 1.75×1.6×1.15 | 2.6 | |
SF-4 | 4 | 2-4 | 15 | 220 | 25 | 1.5 | 1.85×2.05×1.2 | 2.9 | |
SF-8 | 8 | 4-8 | 30 | 191 | 25 | 1.5 | 2.2×2.9×1.4 | 4.2 | |
SF-10 | 10 | 5-10 | 30 | 191 | 25 | 1.5 | 2.2×2.9×1.7 | 4.5 | |
SF-20 | 20 | 5-20 | 30×2 | 191 | 25 | 1.5 | 2.85×3.8×2 | 9.9 | |
JJF type flotation machine |
JJF-2 | 2 | 1-3 | 7.5 | 443 | 25 | 1.5 | 1.4×1.4×1.1 | 1.7 |
JJF-4 | 4 | 2-4 | 11 | 305 | 25 | 1.5 | 1.6×2.15×1.25 | 2.4 | |
JJF-8 | 8 | 4-8 | 22 | 233 | 25 | 1.5 | 2.2×2.9×1.4 | 4.5 | |
JJF-10 | 10 | 5-10 | 22 | 233 | 25 | 1.5 | 2.2×2.9×1.7 | 4.9 | |
JJF-16 | 16 | 5-16 | 30 | 180 | 25 | 1.5 | 2.85×3.8×1.7 | 8.0 | |
JJF-20 | 20 | 5-20 | 37 | 180 | 25 | 1.5 | 2.9×3.8×2.0 | 10.5 |
Technical parameters of BF flotation machine
Model | Trough cubage (m³) |
Inside dimensions (L×W×H) (m) |
Air suction amount (m³/㎡·min) |
Power (kw) |
Motor model | Processing capacity (m³/min) |
Single trough weight (t) |
BF-0.37 | 0.37 | 0.74×0.74×0.75 | 0.9~1.05 | 1.5 | Y90L-4 | 0.2~0.4 | 0.5 |
BF-0.65 | 0.65 | 0.85×0.95×0.9 | 0.9~1.10 | 3.0 | Y132S-6 | 0.3~0.7 | 1.0 |
BF-1.2 | 1.2 | 1.05×1.15×1.10 | 1.0~1.10 | 5.5 4.0 |
Y132M2-6 Y132M1-6 |
0.6~1.2 | 1.4 |
BF-2.0 | 2.0 | 1.40×1.45×1.12 | 1.0~1.10 | 7.5 | Y160M-6 | 1.0~2.0 | 1.8 |
BF-2.8 | 2.8 | 1.65×1.65×1.15 | 0.9~1.10 | 11 | Y180L-8 | 1.4~3.0 | 2.2 |
BF-4.0 | 4.0 | 1.9×2.0×1.2 | 0.9~1.10 | 15 | Y200L-8 | 2~4 | 2.6 |
BF-6.0 | 6.0 | 2.2×2.35×1.3 | 0.9~1.10 | 18.5 | Y225S-8 | 3~6 | 3.3 |
BF-8.0 | 8.0 | 2.25×2.85×1.4 | 0.9~1.10 | 22 30 |
Y225M-8 Y250M-8 |
4~8 | 4.2 |
BF-10 | 10 | 2.25×2.85×1.7 | 0.9~1.10 | 22 30 |
Y225M-8 Y250M-8 |
5~10 | 4.7 |
BF-16 | 16 | 2.85×3.8×1.7 | 0.9~1.10 | 37 45 |
Y280S-8 Y280M-8 |
8~16 | 8.4 |
BF-20 | 20 | 2.85×3.8×2.0 | 0.9~1.10 | 37 45 |
Y280S-8 Y280M-8 |
10~20 | 8.7 |
BF-24 | 24 | 3.15×4.15×2.0 | 0.9~1.10 | 45 | Y280M-8 | 12~24 | 9.2 |